Modifying a Haywood M7 kit
How I used the Haywood kit to produce a model of a push-pull fitted Drummond SR M7 as it was in the early 1960s
Bill Randell
Gazette February 2014 (Vol 19 No.2)
Failed to open database: gaugegu1_gog2 | ret is false |
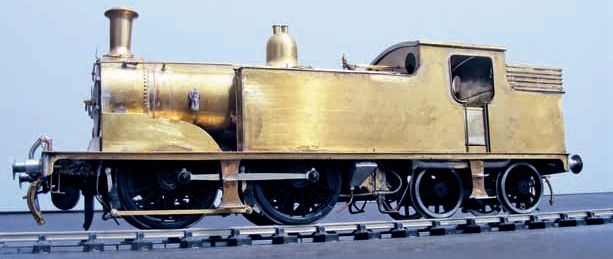
Putting a crank axle into a 0-4-4 was not an easy option. In the 700 it would be possible to drive the rear axle, but the M7 had to have non-working motion but working axle boxes to test the principle of removable motion. This set the basic parameters for my model. There had to be a chassis with sprung axles and a body with pull-push gear and extended bunker coal rails, together with any other extra detail that was visible on the real engine.
I looked at the Haywood kit, starting with the chassis, and it was apparent that the frames would be rather close together if I used the spacers as supplied. Further study of drawings of the engine showed that the frames should be joggled inwards behind the firebox. This provided the solution. I could keep the back end as designed and joggle the frames behind the firebox position to the maximum possible width between the driving wheels. This was done by gluing 1mm thick steel to the frame positioned so that, when the frame was squeezed in a vice, the frame was bent but the front and back sections remained parallel. When the shims were removed and the rear frame spacer fitted the frames were 22.5mm apart at the rear and 24.5mm apart at the front which was just enough to be able to fit the motion.
The deviations from the designed method of construction meant that there had to be some changes to the chassis and the running plate. A strip of 0.7mm nickelsilver, 24.5mm wide, was cut from sheet.
This provided material to make new frame spacers, the motion bracket and the rear of the cylinder block. The central part of the running plate from the drivers to the original fixing hole below the smokebox was cut out to make space for the motion and cylinder block. The etched positions for the hornguides were cut out in the frames, and then the basic chassis was soldered together.
Meteor Models hornguides were drilled and tapped to take 12BA screws to enable me to adjust the ride height. At the foot of each casting the cast web was removed and a short piece of tube, tapped 12BA, was soldered on to take the keepers when they were fitted. The axle boxes have a square body and a turned extension. These extensions prevented the fitting of the gearbox on the driven axle and of the slidebars next to the leading axle, so each box was mounted in a 4-jaw chuck and centred with reference to the turned portion.
The extension was then turned down and the square portion reduced until the box and hornguide were the same thickness. The hornguides were positioned using dummy axles and, once I was happy that they were square and level in the frames, they were soldered in position. Two axle boxes were drilled and tapped to match the ride adjusting screws and two boxes were drilled to take a brass peg. The boxes with pegs were used on the driving axle with the spring located by the peg and the ride height screw, all retained by a plain keeper. The front axle was sprung from below with a headless screw passing through the keepers and serving as the spring pillar. Each box was reamed to remove any burrs.
The next stage was to make the motion
together with the motion bracket and rear
face of the cylinder block. Four bar
Stephenson inside motion from Laurie
Griffin Miniatures was used for the
components, and these were cleaned up
and test assembled to establish the spacing
of the valve chest and cylinder centres. Checking the fit of the slidebars and valve rod guides
As in the prototype the valve chest had to be cut into the cylinder covers by the width of the bolting flange cast into the cylinder cover, and the valve chest casting had to be turned down to the diameter over the valve glands. These castings were sweated onto a strip of nickel silver to form the rear face of the cylinder block. This assembly was drilled to take the piston and valve rods. Centres measured from this assembly were used to mark the centres in the motion bracket, which was then cut out to accommodate the slide bars and the valve rod guides. The various bits of the valve gear were then tried in position, and once they all worked they were soldered into the frames.
At this point I now had a very nice representation of the inside motion that fitted into the body but there were three glaring faults. First, it was very obvious that the wheels were behind the line of the splashers and cruelly exposed. The second was the motion bracket floating about partially above the line of the frames.
Finally, the weigh shaft needed to be positioned in mid-air. The solution was to produce extensions to the frames that matched the profile of the real ones and to widen the splashers. This gave me a chassis that looked right and worked. After some testing on the rails to ensure that the chassis worked as a vehicle, I finished off the detail of brakes and injectors.
With the drivers sprung I found that the extra flexibility of a sprung bogie was needed to help road holding and allow some fine adjustment of the load on the drivers. The bogie frame supplied was meant to be pivoted horizontally on a fixed frame. I changed this by leaving the rubbing plate free to move vertically on the fixing screw and placing a spring, chosen by trial and error, to push the plate down onto the bogie so that the back of the loco was lifted slightly.
To give each axle some independent vertical movement I attached the wheel bearings to the compensating beams I had fabricated to give the bogie a more realistic appearance. These were pivoted on a rod soldered under the bogie frame and the bearing holes in the frame were extended so that the axles could rise and fall by about 1mm. When all the bodywork, including the extra detail I intended to add, was finished, the loco was balanced by adding weight in the bunker to bring the footplate level.
The body was built as intended except in the area of the cab and bunker. The bunkers of the M7s in later years had 5 plated-in coal rails. Scrap fret was used to produce the two extra rails which were soldered, together with the three rails provided, to a thin backing plate 11.5mm wide which brought the bunker up to the correct height.
The cab in the kit is rather bare so the tank extensions and seats and the shaped bunker front were fabricated from sheet brass. Hinged cab doors were added to match my chosen engine followed by the steam reverser lever, pull-push regulator handle, damper handles, gauges and a backhead. Laurie Griffin’s push-pull fittings were fitted, using copper wire of various thicknesses to represent the pipework. As I happened to have brass castings for the chimney and dome these were used instead of the ones provided. The castings provided in the kit would have been adequate, albeit taking longer to bring to a fine finish. One problem I encountered with the push-pull gear was fitting the main air reservoir under the front frames. It needed two straps to suspend it from the chassis.
New cab doors and extended bunker
Making straps and providing anchors on the chassis seemed so simple but the reservoir is a very nice solid brass turning. No means of soldering known to me would fix those straps to such an effective heat sink. If the reservoir was hot enough everything else would come adrift. In the end I resorted to the use of super glue to fasten the reservoir to the straps followed by a little araldite for a strong joint. After the hard work I had a model that I think looks the part and the finished model runs well with an ABC motor and gearbox.
Track holding has proved to be exemplary and it will pull eight heavy coaches with ease. The valve gear took no more time than outside motion and gives the hint that there are ‘works’ that make it move. I did learn that my initial thoughts of using plunger pick-ups on the 700 may not be practical but I will be solving that problem as soon as the M7 is painted.
To help me to create the model I found three books very helpful:
LSWR Locomotives, The Drummond Classes, by D L Bradley (Wild Swan Publications) has drawings of the long frame M7 which shows the bogie equalising beams, the shape of the tanks and bunker front and the positions of the motion bracket and cylinder chest.
The Book of the M7 0-4-4Ts by Peter Swift (Irwell Press Ltd.) has detailed views of all members of the class including the underside of 672 when it fell down the wagon lift at Waterloo.
From Nine Elms To Swanage, The Story of M7 Class No 30053 (The Drummond Locomotive Society) has views of the chassis showing the motion bracket and of the cab interior.