© Raymond Walley – All rights reserved. Transferred to Wiki by Tommy day
CAMBRIAN RAILWAY BRAKE VAN
This wagon was produced and reviewed by Raymond under the Dragon Models name. Dragon Models are now known as Taff Vale Models and are under new ownership
Failed to open database: gaugegu1_gog2 | ret is false |
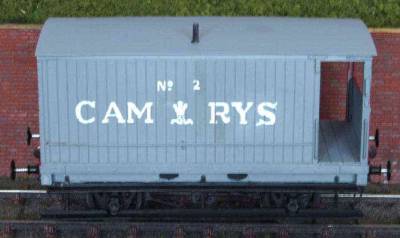
This is the next
vehicle in a train
of eight for a
client. It arrived
from the client in
a box partially
started but I
believe normally
comes as a flat
pack. The
instructions cover
six sides of A4
and include a
series of coloured
construction
pictures, some
prototype
information, a
dimensioned drawing and an additional couple of pages of prototype
information. Here are most of the parts laid out ready to start with the addition
of Slater's wheels and WEP compensation units.
The recommended start is to fit the sole bars and then the inner partition
however, looking ahead, I decided it would be easier to fit the ends and a side
first and then fit the partition. That way it can be correctly lined up with the end
of the cabin and avoid the natural tendency of fitting it in the etched line of a
floor plank. The ends needed the fold over that represent the buffer beam filing
down somewhat so that they are a snug fit against the sole bars. Once done, it is
a simple matter to solder them up square. Well, it should be but, as you can see
in the next picture, I did not quite make it and had to go back and straighten up
one corner.
The sides also
need some work
with a file to
open out the
notches at the
bottom corner so
that they are a
good fit around
the buffer beam.
Actually, a good
fit is not essential since they are covered by strapping plates later. I also left
fitting the long handrails until the body was assembled so that it would lie flat
on the bench when soldering. Normally I fit as much as possible in the flat but
this was one time that that was not appropriate. It is necessary to cut away a
small section of the upper fold over on the sides so that the partition will fit. I
also found that
this partition was
too tall and
needed filing
down a little to
get the roof to fit.
Here is the floor
before the ends
and sides were
fitted and you
can see that
several cut outs
were necessary
for the axle
guards and V
hangers to fit
perpendicular to it. The instructions do not mention this, but careful study of
the pictures reveals that something similar was done on the demonstration
model. It would have been much easier to have done this before soldering the
sole bars.
The cut-outs need to be about a millimetre deep. Ensure also that the ends of
the completed floor are filed off square, or the van ends will not sit properly,
which in turn will cause the sides to fall short of the ends. Dry runs are
recommended. Some of the parts are etched slightly over size, hence the need
to check and adjust, but better than being too small. The next job is to fit the
underframe detail. Checking the axle guards against the suspension units
indicated that they needed a 2mm thickness of packing to line up the holes with
the axles.
This small
problem was
overcome by
soldering some
short lengths of
rectangular brass
tube on the floor,
to which the
compensation
units were then
soldered. The
tube did not
require the vast
amounts of heat
that solid section
would have.
The underframe
detail is pretty
standard, now all
that is required
are the springs,
hangers and axle
boxes fitting.
The springs and
hangers come as
separate items
and clearly are
intended to be
fixed inside the
sole bars.
Unfortunately,
this is not
possible due to
the W irons being
in the way. I
used Loctite 408
to fix the springs
into the hangers and then cut away the remainder of the hanger portion so that
the combined spring and hangers could be fixed to the W irons with 408.
The axle boxes also need to have
their backs filed down flush to
be fixed to the W irons.
Here, the three parts have been fitted
to vehicle.
Completed and
awaiting a trip to
Dennis's paint
shop, after which
the glazing can
be fitted and the
roof firmly fixed.